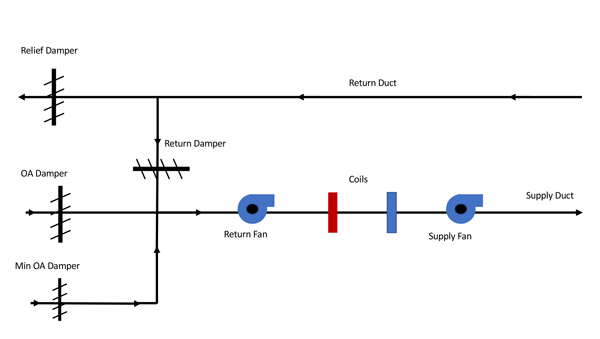
Lesson Learned in Project Performance
Garrett Holland April 5, 2019
WorkingBuildings has acquired considerable knowledge in the course of project performance. In many cases, these lessons learned have been used to prevent the same issues from occurring on additional projects. The actual list of lessons learned is too lengthy to include in total, but here are a few examples of lessons learned from past projects:
An airside economizer is often used for energy savings when allowed by outdoor conditions. One project demonstrated that the configuration of the return fan, relief damper, return damper are crucial in order to maintain the building pressure while acting as a partial airside economizer. In this case, the configuration had the return fan installed in the AHU, and the return damper and relief damper installed in the return duct. However, when the return fan is installed in the AHU, the relief damper should also be installed in the AHU between the supply and return fan to allow for building pressure relief. When the AHU was modulating the relief damper in partial economizer to maintain the building pressure, air was being pulled back into the return duct through the relief damper. This was caused because the return fan was not in a location to force air out the relief damper, and only acted as a second supply fan. As a result, the building pressure was extremely positive, causing the exterior doors to stand open when the AHUs were partially acting as an airside economizer.
Lighting controls integration with mechanical controls is often used for energy savings. In the event that the light occupancy sensors detect occupants, the mechanical equipment serving those spaces will go into occupied mode until the light occupancy sensor no longer detects occupants, and the mechanical equipment will go into unoccupied mode. It was found during several projects there was no coordination between the electrical and mechanical design teams to instruct contractors on how the mechanical systems will be tied to the lighting control system. This results in a scope gap, and the owner will not achieve the energy savings that were originally anticipated. Subsequently, WorkingBuildings has found it extremely beneficial to ensure that both mechanical and electrical design teams have coordinated on the intent of design for the lighting control system and work together to assure that the contract documents reflect this coordination.
Sizing and application of equipment is crucial, especially when being used in critical spaces like a compounding pharmacy. In one case, the equipment sized for design required that the discharge air temperature of a rooftop unit be 48ºF throughout the year. The equipment submitted was able to make 48ºF at the discharge of the cooling coil during low load conditions. However, the rooftop unit also utilized hot gas reheat, and could only maintain a supply air temperature of 55ºF. Hot gas reheating works by taking hot refrigerant and running it through a reheat coil located after the cooling coil in the rooftop unit, instead of running all of the refrigerant through the condenser. This allows for energy savings in situations where reheating is acceptable. On this project, the discharge air temperature and space temperature and humidity are critical, and without the proper space conditions, pharmaceuticals can become contaminated. WorkingBuildings has learned during the submittal review process and design review process that space conditions can be met by proper usage of the designed and contractor submitted equipment.
These are just a few examples of lessons learned through projects, and how these issues can be avoided. Passing this knowledge on to our clients can save them money, time, and stress.